
Military Glove Development
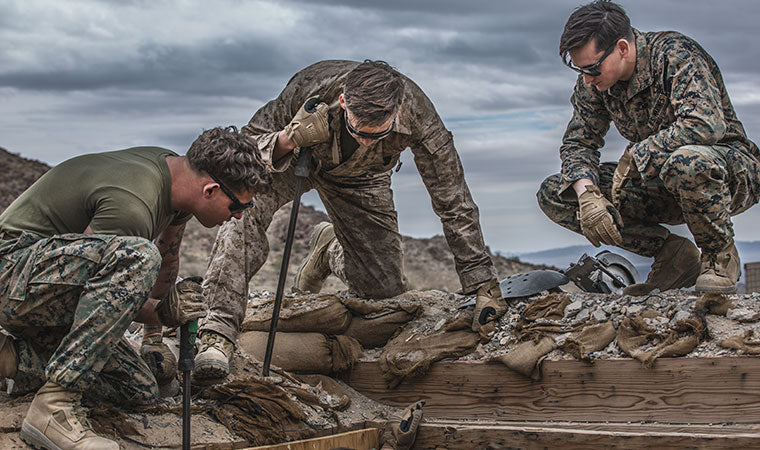
Training Time
Training and drills are a common component of military service. The best training takes place in simulated battlefields whose conditions mirror what soldiers can expect to encounter in a real battle. Just like in a real battle, there is a level of destruction expected during those exercises.
Two years ago, our team visited with the US Marine Corps. and got to meet the men and women responsible not only for building those simulated battlefields but also for cleaning up some of the mess left behind when the dust clears and the training is over, the RTAMS personnel. Learning firsthand by working side by side with these Marines, our team got to experience the real life conditions and the challenges they face when performing their duties.

The Challenges
Part of their duties involve building armored bunkers like you often see in war movies. Unlike the movies with their painted spray-foam covered plywood and plastic “barbed wire”, the Marines work with the real thing: reinforced concrete, steel, razor, barbed, and concertina wire.
During preparation of the practice fields they deal with abrasive materials that wear through regular protective gloves, sharp metal blades that slice through even the toughest leather range gloves, heavy objects that cause impact injuries, and piercing hazards that push between the weaves of standard woven and dipped gloves. When the dust settles, it is more of the same with extra jagged bits and shards thrown in for added flavor. And to top it all off, there’s the heat to contend with that makes wearing gloves for 8+ hours a day less than ideal.
We dove in. We saw what these conditions did to the best PPE they had available and listened to the military personnel’s suggestions on what would meet their particular needs so their people could get the job done quickly and most importantly, safely.
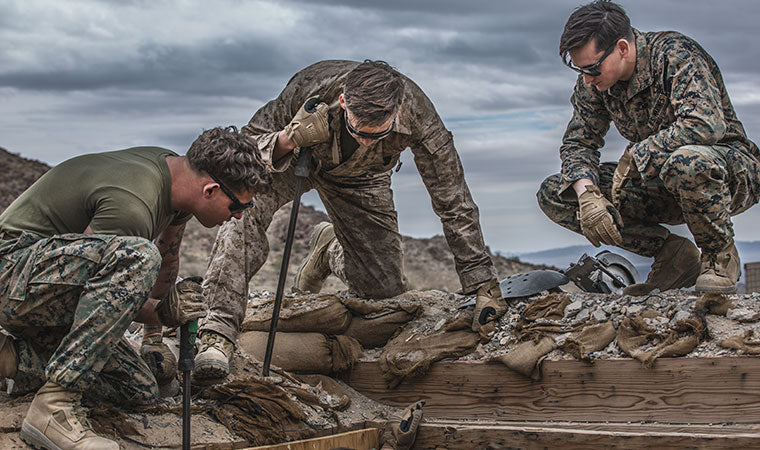
The Drawing Board
Most situations requiring PPE are focused on only one or two hazards at a time. A recycling center worker might only need cut and puncture protection while a construction worker would be more interested in impact and abrasion for instance. Here we had a challenge that called for a glove that could protect their wearer from just about anything: impacts, cuts, punctures, abrasions, and tears, all while being comfortable to wear and not impeding fine motor control.
We went through 4 different prototype designs that all failed to adequately meet these criteria before we found a suitable solution that we felt met the needs of our servicemen and women. To ensure that we delivered the best possible protective glove, we wanted to test it under actual use conditions and see if it really did live up to what we claimed. So to validate this solution and to show that we stand fully behind the quality of our products, we revisited the original field and tested our items ourselves in the same conditions that they would be put to use.
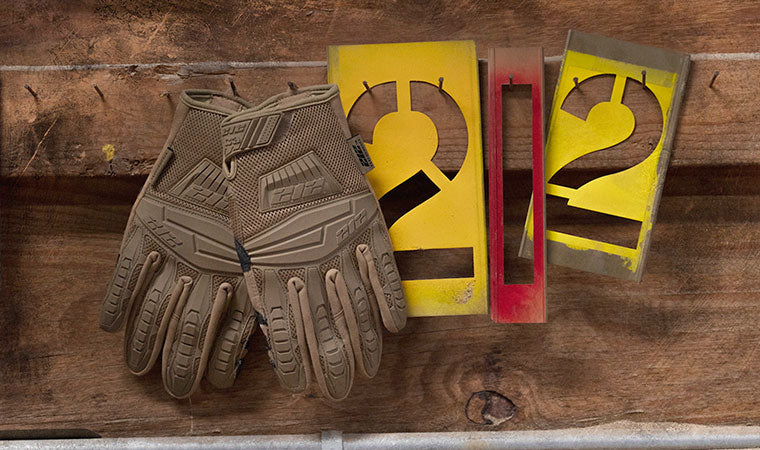
The Result
Our design lived up to expectations. Still, we firmly believe that the perfect protection solution is yet to be found. To that end, we continue to refine and perfect our products to bring the best protection possible to our men and women in uniform. This first effort has so far yielded 6 brand new items designed and engineered specifically for the demanding challenges of military use and we will continue to pursue the development of as many more as we need to so that everyone can work safer today than they did yesterday.
Shop Military Gloves